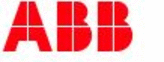
グループ: ABB
カタログの抜粋
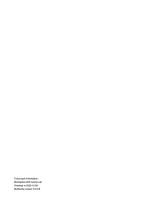
Trace back information: Workspace 22D version a8 Checked in 2022-12-09 Skribenta version 5.5.019
カタログの2ページ目を開く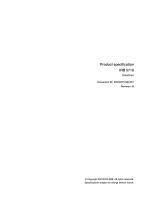
Product specification IRB 5710 OmniCore Document ID: 3HAC075188-001 Revision: B © Copyright 20212022 ABB. All rights reserved. Specifications subject to change without notice.
カタログの3ページ目を開く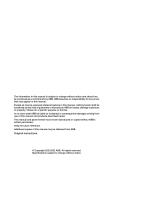
The information in this manual is subject to change without notice and should not be construed as a commitment by ABB. ABB assumes no responsibility for any errors that may appear in this manual. Except as may be expressly stated anywhere in this manual, nothing herein shall be construed as any kind of guarantee or warranty by ABB for losses, damage to persons or property, fitness for a specific purpose or the like. In no event shall ABB be liable for incidental or consequential damages arising from use of this manual and products described herein. This manual and parts thereof must not be...
カタログの4ページ目を開く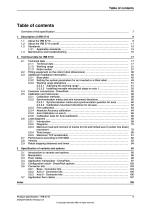
3HAC075188-001 Revision: B © Copyright 20212022 ABB. All rights reserved.
カタログの5ページ目を開く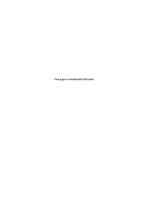
This page is intentionally left blank
カタログの6ページ目を開く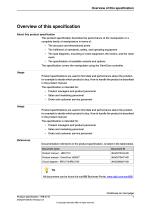
Overview of this specification Overview of this specification About this product specification This product specification describes the performance of the manipulator or a complete family of manipulators in terms of: • The structure and dimensional prints The fulfilment of standards, safety, and operating equipment The load diagrams, mounting or extra equipment, the motion, and the robot reach The specification of available variants and options The specification covers the manipulator using the OmniCore controller. Usage Product specifications are used to find data and performance about the...
カタログの7ページ目を開く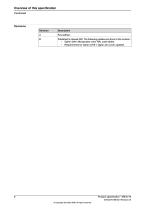
Overview of this specification Continued Revisions Revision First edition. Published in release 22D. The following updates are done in this revision: • Option 209-x Manipulator color RAL code added. • Requirements for option 3316-1 Upper arm cover updated. Product specification - IRB 5710 3HAC075188-001 Revision: B © Copyright 20212022 ABB. All rights reserve
カタログの8ページ目を開く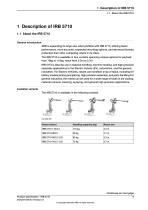
1 Description of IRB 5710 1.1 About the IRB 5710 General introduction ABB is expanding its large size robot portfolio with IRB 5710, offering faster performance, more accurate, expanded mounting options, and advanced foundry protection than other competing robots in its class. The IRB 5710 is available in four variants spanning various options for payload from 70kg to 110kg, reach from 2.3m to 2.7m. IRB 5710 is ideal for use in material handling, machine tending, and high precision assembly applications in the Electric Vehicle (EV), automotive, and the general industries. For Electric...
カタログの9ページ目を開く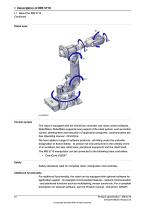
1 Description of IRB 5710 1.1 About the IRB 5710 Continued Robot axes Control system The robot is equipped with the OmniCore controller and robot control software, RobotWare. RobotWare supports every aspect of the robot system, such as motion control, development and execution of application programs, communication etc. See Operating manual - OmniCore. We have added a range of software products - all falling under the umbrella designation of Active Safety - to protect not only personnel in the unlikely event of an accident, but also robot tools, peripheral equipment and the robot itself....
カタログの10ページ目を開く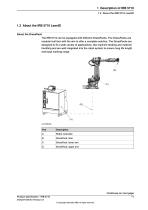
1 Description of IRB 5710 1.2 About the IRB 5710 LeanID 1.2 About the IRB 5710 LeanID About the DressPack The IRB 5710 can be equipped with different DressPacks. The DressPacks are modular built but with the aim to offer a complete solution. The DressPacks are designed to fit a wide variety of applications, like machine tending and material handling and are well integrated into the robot system to ensure long life length and large working range. Robot controller DressPack, floor Continues on next page Product specification - IRB 5710 3HAC075188-001 Revision: B © Copyright 20212022 ABB. All...
カタログの11ページ目を開く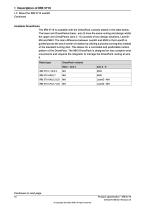
1 Description of IRB 5710 1.2 About the IRB 5710 LeanID Continued Available DressPacks The IRB 5710 is available with the DressPack variants stated in the table below. The lower arm DressPacks (base - axis 3) have the same routing and design whilst the upper arm DressPacks (axis 3 - 6) consists of two design solutions, LeanID MH and MH3. The main difference between LeanID and MH3 is that LeanID is guided across the axis 6 center of rotation by utilizing a process turning disc instead of the standard turning disc. This allows for a controlled and predictable motion pattern of the DressPack....
カタログの12ページ目を開く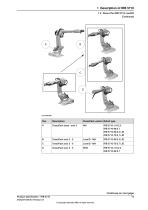
1 Description of IRB 5710 1.2 About the IRB 5710 LeanID Continued DressPack variant Robot type DressPack base - axis 3 Continues on next page Product specification - IRB 5710 3HAC075188-001 Revision: B © Copyright 20212022 ABB. All rights reserved.
カタログの13ページ目を開く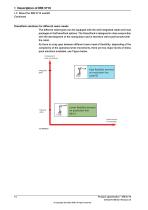
1 Description of IRB 5710 1.2 About the IRB 5710 LeanID Continued DressPack solutions for different users needs The different robot types can be equipped with the well integrated cable and hose packages in theDressPack options. The DressPack is designed in close conjunction with the development of the manipulator and is therefore well synchronized with the robot. As there is a big span between different users need of flexibility, depending of the complexity of the operation/wrist movements, there are two major levels of dress pack solutions available, see Figure below. Complexity in wrist...
カタログの14ページ目を開く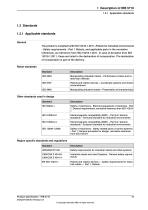
1 Description of IRB 5710 1.3.1 Applicable standards 1.3 Standards 1.3.1 Applicable standards General The product is compliant with ISO 10218-1:2011, Robots for industrial environments - Safety requirements - Part 1 Robots, and applicable parts in the normative references, as referred to from ISO 10218-1:2011. In case of deviation from ISO 10218-1:2011, these are listed in the declaration of incorporation. The declaration of incorporation is part of the delivery. Robot standards Standard Manipulating industrial robots – Performance criteria and related test methods Robots and robotic...
カタログの15ページ目を開く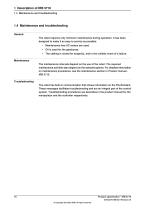
1 Description of IRB 5710 1.4 Maintenance and troubleshooting 1.4 Maintenance and troubleshooting General The robot requires only minimum maintenance during operation. It has been designed to make it as easy to service as possible: • Maintenance-free AC motors are used. The cabling is routed for longevity, and in the unlikely event of a failure. Maintenance The maintenance intervals depend on the use of the robot. The required maintenance activities also depend on the selected options. For detailed information on maintenance procedures, see the maintenance section in Product manual IRB...
カタログの16ページ目を開く