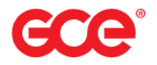

カタログの抜粋
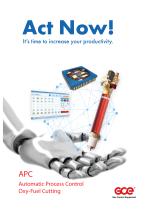
It's time to increase your productivity.
カタログの1ページ目を開く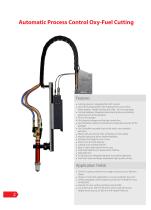
Features • Cutting process is integrated into APC system • Oxy-Fuel Cutting System with Cutting Torch, Gas Control, Flame Ignition, Height Sensing and Lifter - all in one package • Cutting database, integrated automated ignition, preheating piercing and cutting operation • Fits on all carriages • Only requires oxygen and fuel gas connection • Gas distribution, safety and electrical components are part of the package • Gas Controller mounted close to the torch, one controller per torch • Works with all common CNC controllers on the market • Modular approach allows highest flexibility •...
カタログの2ページ目を開く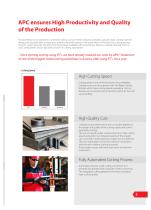
APC ensures High Productivity and Quality of the Production The best Return on Investment is when the cutting cost per meter is kept low. Besides using the right cutting machine design and using the best components, another important aspect is the automation of the Oxy-Fuel cutting process. The APC system provides the best torch technology available with extraordinary features, carefully selected ˝best in class˝ components and a high level of Oxy-Fuel cutting automation. ˝ Since starting cutting using FIT+ we have already reduced our costs by 28%.“ Statement of one of the biggest metal...
カタログの3ページ目を開く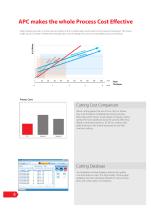
APC makes the whole Process Cost Effective When looking at costs, it is the cost per metre of the cut that really counts and not the overall investment. This cost is made up of a number of elements including the cost of energy, the cost of consumables and cost of labour. Plate Thickness Process Costs Cutting Cost Comparison When cutting plates that are 20 mm (3/4”) or thicker, Oxy-Fuel should be considered as primary process. New high performance nozzle design increases cutting speed, the most significant factor for process efficiency. Based on the latest statictics, 20-50 mm carbon steel...
カタログの4ページ目を開く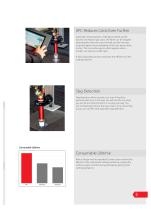
APC Reduces Costs Even Further Automatic internal igniton of the flame speeds up the process and reduces gas costs. The flame can be stopped automatically when the cut is finished and then be easy re-ignited again when preheating of the next piece needs to start. This is a similar way to what happens when a modern car stops at a traffic light. A fully automated process maximises the efficiency of the cutting machine. Slag Detection Slag detection allows a perfect cut even if slag from previous piercing is in the way. You will lose the cut when you do not act while the torch is moving over...
カタログの5ページ目を開く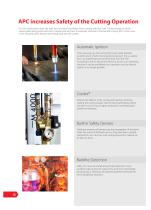
APC increases Safety of the Cutting Operation It is very important to have the right level of safety knowledge when cutting with Oxy-Fuel. Full knowledge of all the various gases being used and how to handle and use them is especially important. One benefit of using APC is that many of the required safety features are already built into the system. Automatic Ignition “Every site using Oxy-Fuel cutting that I have visited, reported accidents due to faulty manual ignition processes”, this is a quote from an experienced service technician from the USA. According to the EU Machinery Directive,...
カタログの6ページ目を開く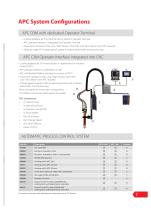
APC O3M with dedicated Operator Terminal • Cutting database for FIT+ three torches is stored in Operator Terminal • APC operator interface is integrated into Operator Terminal • Hassle free interface to CNC, only "Start Process” from CNC and "Ok to Move” from APC required • Optional usage of "Change Speed” output to reduce speed while moving over slag • Cutting database for FIT+ three torches is implemented in machine control (CNC) • APC operator interface is embedded in CNC • APC with flexible fieldbus interface to connect to CNC* • Hassle free interface to CNC, only "Start Process” from...
カタログの7ページ目を開く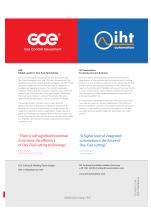
GCE Global Leader in Oxy-Fuel Technology IHT Automation Focussing on Core Business GCE is a world leading company in the field of Oxy-Fuel and Gas Control Equipment with over 100 years of experience in the handling of industrial, medical and specialty gases. The GCE Group has grown rapidly since its creation and now is a leader in the European gas equipment industry. The Group’s Headquarter is based in Malmö, Sweden. The major manufacturing centres are located in the Czech Republic, China and Germany. Worldwide the Group now employs in excess of 950 people who are all ready to fulfil the...
カタログの8ページ目を開くGCE Groupのすべてのカタログと技術パンフレット
-
APTECh
8 ページ
-
MASS FLOW CONTROLLER
16 ページ
-
GCE GROUP VALVES
12 ページ
-
MEDIVITOP®
4 ページ
-
GCE CENTRAL GAS SYSTEMS
408 ページ
-
HEALTHCARE CATALOGUE
64 ページ
-
MEDIVITAL®
4 ページ
-
CENTRAL GAS SUPPLY
48 ページ
-
HP DRUVA CATALOGUE
49 ページ
-
Zeno_Brochure
8 ページ
-
MEDICAL CENTRAL GAS
48 ページ
-
HEALTHCARE CATALOGUE
44 ページ
-
VALVES
12 ページ
-
Leaflet_Suction_jars
2 ページ
-
Zeno_lite
2 ページ
-
MFC CATALOGUE
16 ページ
-
TECHLINE CATALOGUE
48 ページ
-
speciality gas equipment
112 ページ
-
MEDIEVAC+
2 ページ
-
Medivital
4 ページ
-
VARIMED
2 ページ
-
MEDISELECT® II
4 ページ
-
MEDIEJECT PLASTIC
2 ページ
-
NUVO 8
2 ページ
-
APS II
4 ページ
-
GSS
2 ページ
-
MM90 - HP UNIT AUTO
2 ページ
-
PRESSURE WATCH DN20
4 ページ
-
GCE MEDIUNIT CZ TYPE
2 ページ
-
GAS ALARM MC7701
2 ページ
-
GAS ALARM G4
2 ページ
-
GAS ALARM C44
2 ページ
-
MEDIWET
2 ページ
-
Medimeter
2 ページ
-
MediEject
2 ページ
-
BAG VALVE MASK
2 ページ
-
Inogen One® G3
2 ページ
-
Inogen One® G2
2 ページ
-
Elite
2 ページ
-
ECOlite® 4000
2 ページ
-
EASE II
2 ページ
カタログアーカイブ
-
MEDIEVAC+ Old
2 ページ