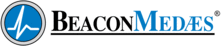

Catalog excerpts
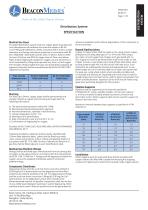
Distribution System SPECIFICATION DISTRIBUTION SYSTEM Pipe outside diameter (mm) Pipe outside diameter (mm) Medical Gas Pipes The piped distribution system shall use copper pipes manufactured from phosphorous de-oxidised non-arsenical copper to BS EN 1412:1996 grade CW024A (Cu-DHP), manufactured to metric outside diameters and having mechanical properties in accordance with BS EN 13348:2008 - R250 (half hard) for sizes 12-28mm, R250 or R290 for sizes 35-54mm and R290 for larger sizes of 76mm and above. Pipes shall be degreased suitable for oxygen use and cleanliness is to be maintained by filling each pipe with dry, clean, oil and oxygen free nitrogen, fitting suitable end caps and protectively wrapping. All pipework materials shall be manufactured by BS EN ISO 9001:2001 registered companies. Marking For sizes up to 54mm, copper pipes shall be permanently and durably marked at regular intervals along its length with the following information: a) The harmonised standard number EN 13348; b) BSI kitemark/statement/equivalent approval; b) Nominal dimensions, diameter x wall thickness; e) Date of production: year and month (1 to 12) f) Confirmation of degreasing for oxygen; Example: BS EN 13348 22x0.9 R250 WIELAND LAWTON KITEMARKED DEG/MEDICAL 05 01 Following installation, pipelines shall be clearly identified with 150mm wide adhesive labels. Labels shall be fitted near walls, risers, valves and junctions. Colour coding and labelling shall be in accordance with BS 1710:1984. Arrows to identify the direction of gas flow shall be fitted adjacent to each identification label. Medical Gas Pipeline Fittings Fittings shall be end feed type, manufactured from the same grade of copper as the pipes and be in accordance with the requirements of BS EN 1254-1:1998 Part 1. Fittings shall be degreased suitable for oxygen use and be supplied individually sealed in protective polythene bags. Component Cleanliness Degreasing of pipe shall be such that there is less than 20mg/m2 (0.002mg/cm2) of hydrocarbons on the degreased surface when tested by the method specified in EN 723. The degreasing of fittings shall be such that there is less than 100mg/m2 (0.01mg/cm2) of hydrocarbons on the degreased surface when tested by the aforementioned method. All pipeline components shall also be free of any visible liquid detergent washing or solvent degreasing. Other methods may be used if they are proven and can be guaranteed to achieve acceptable results without degradation of the component or the environment. Brazed Pipeline Joints Copper to copper joints shall be made on site using a silver-copper-phosphorous brazing alloy type CP1 or CP4 to BS 1845 using a dry, clean, oil and oxygen free nitrogen inert gas shield with no flux. Copper to brass or gunmetal joints shall not be made on-site. Copper to brass or gunmetal joints made off-site shall utilise silver brazing material type AG13 to AG18 to BS 1845 with a flux. Such shall joints be subsequently cleaned and degreased prior to use. Where pipes are cut on site they shall be cut clean and square with the pipe axis, using wheel cutters where possible and deburred, re-rounded and cleaned off. Expanded joints shall only be used for straight pipe joints and shall not be used for pipes sizes greater than 28mm outside diameter. Expansion joints shall only be made using apparatus specifically designed for the purpose. Pipeline Supports Pipelines shall be supported at the intervals specified in HTM2022/02-01 using a suitable metallic, non-ferrous material or a ferrous material suitably treated to prevent corrosion and electrolytic action. Plastic supports shall only be used for support of drops to terminal units. Maximum intervals between pipe supports as specified in HTM 2022/02-01: Installation Where pipeline pass through walls they shall be provided with copper sleeves and filled with suitable intumescing fire stopping compound. Pipeline joints shall not be located inside copper sleeves. Atlas Copco Ltd. trading as Atlas Copco Medical Unit 18 Nuffield Way, Abingdon, Oxfordshire, UK OX14 1RL www.beaconmedaes.com
Open the catalog to page 1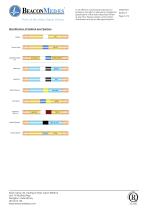
Part of the Atlas Copco Group Identification of Medical Gas Pipelines In an effort to continuously improve our 2002018.9 products, the right is reserved to change the 04/05/17 specification of the items described herein at any time. Please contact us for further information and up to date specifications. Medical Vacuum Nitrous Oxide Atlas Copco Ltd. trading as Atlas Copco Medical Unit 18 Nuffield Way, Abingdon, Oxfordshire, UK OX14 1RL www.beaconmedaes.com
Open the catalog to page 2All BeaconMedaes catalogs and technical brochures
-
Series B Premium
3 Pages
-
Local alarm
4 Pages
-
Central alarm
4 Pages
-
Digital Medical Gas Alarms
4 Pages
-
Zone Valve Boxes
4 Pages
-
mVAC Medical Vacuum Systems
8 Pages
-
Medical Scroll Air Retrofit
4 Pages
-
Ceiling Columns
2 Pages
-
Medical Vacuum Filters
4 Pages
-
Claw Medical Vacuum
8 Pages
-
Hose Assemblies
2 Pages
-
Biomaster Additive
4 Pages
-
Medical Gas Outlets
4 Pages
-
Lifeline Manifolds
4 Pages
-
Medical Equipment Air
8 Pages
-
Medical Instrument Air
4 Pages
-
ZMED Medical Air Systems
6 Pages
-
Scroll Medical Air Systems
8 Pages
-
Medical Air Dryers
2 Pages
-
Magnis MSV
2 Pages
-
mVAC
12 Pages
-
Lifeline® MCS
5 Pages
-
VAV05D-060H-D_V
4 Pages
-
VHV05D-060H-D_V
4 Pages
-
Medical Gas Retrofit Alarm
2 Pages
Archived catalogs
-
Medical Gas Alarm Systems
4 Pages
-
Medical Gas Outlets_2009
4 Pages
-
Oxygen and Air Flowmeters
2 Pages
-
Suction & Oxygen Therapy
2 Pages
-
Medical Air Desiccant Dryers
2 Pages
-
Instrument Air White Paper
39 Pages
-
Z MED Medical Air Systems
6 Pages
-
Claw Vacuum System
6 Pages