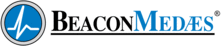

Catalog excerpts
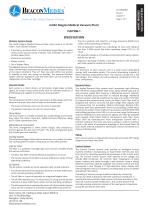
BeaconMed/es Part of the Atlas Copco Group mVAC Magnis Medical Vacuum Plant ISO7396-1 U D S3 E5 SPECIFICATION Modular System Design The mVAC Magnis Medical Vacuum Plant shall conform to EN ISO 7396-1. Each system includes: • From two to six direct driven, oil-lubricated, single stage, air cooled rotary screw vacuum pump modules, fully enclosed, each with a variable speed drive • Vertical air receiver(s) • Master control • Set of duplex filters The Medical Vacuum Plant shall ensure the minimum pipeline vacuum level of 450mmHg is maintained at the plant service connection point at the rated volumetric 'free air' flow rate with either two pumps in standby or with one pump on standby. The bacteria filtration system shall be 'duplexed' such that each filter can be isolated for replacement of the filter cartridge. • The oil is synthetic and rated for a change interval of 8,000 hours under normal operating conditions. • The oil separation system has a discharge oil carry over rating of less than 3 PPM across the entire operating range (1013 to .35 mbar). • Oil separator design is of multiple vertical elements, easily replaceable by one person. • Separator discharge includes a drip leg internal to the enclosure with drain piped to outside of enclosure. Enclosure The enclosure of each vacuum unit is a steel sound attenuating canopy with removable panels. The sound attenuating material is flame retardant polyurethane foam. The vacuum canopy has a hot cold design, that isolates all heat producing components from all other components. Vacuum Pumps Each pump is a direct driven, oil lubricated, single-stage, variable speed, air cooled rotary screw pump with an ultimate pressure of 0.35mbar(a) and capable of continuous duty operation. Airend: The compression profile is of an asymmetric profile design with four lobes on the male rotor and six lobes on the female rotor. • The male and female rotors are the same in diameter. • The element housing is of cast iron construction. Drive Motor: The drive motor is a totally enclosed, fan cooled design and inverter duty rated. The motor meets IE3 / NEMA Premium Efficiency rating and is 100% maintenance free. Motor/Airend Connection: The drive arrangement is direct driven design, fully enclosed to protect against dirt and dust intrusion. The drive arrangement does not include gear box reduction. Cooling System: The vacuum package is fitted with an aluminum, air-cooled, oil cooler. The cooling system includes a temperature controlled axial fan. Inlet Air Filter: The filter is a polyester cartridge type and is factory installed inside the vacuum enclosure. • The filter has 99%+ removal efficiency standard to 5 micron. • The service interval of the filter is at least 4,000 hours under normal operating conditions. Oil System: The oil system includes an air/oil separator with oil level indicator. • The service interval of the separator element is at least 4,000 hours under normal operating conditions. • The oil filter is a spin-on type with an integrated bypass valve. • The oil filter element has a 12 micron beta 75 rating and the service interval is at least 4,000 hours under normal operating conditions. • The oil temperature is regulated by means of a thermostatic bypass valve, and oil circulation is achieved through differential pressure. Bacteria Filters The duplex Bacteria Filter system shall incorporate high efficiency filter elements using stainless steel cores, epoxy sealed caps and an anti-corrosive coated filter housing. A differential vacuum indicator shall be installed across the filter to indicate blockage. Additional pressure sensors shall be installed at the inlet and outlet of the filter to measure the pressure drop across the filters. Each filter shall be designed and sized to carry the full plant design flow capacity with a pressure drop not exceeding 33mbar (25mmHg). Bacteria Filter elements shall have penetration levels not exceeding 0.005% when tested by the sodium flame method in accordance with BS 3928:1969 and utilising particles in the 0.02 to 2 micron size range. Performance shall be validated by a third party test agency and shall be available upon request. Drain flasks shall be connected to each filter. Drain flasks shall be manufactured from transparent Pyrex® with a polymer coating on the inner and outer surfaces in order to maintain a seal in the event of inadvertent breakage of the Pyrex® flask. All drain flasks shall be suitable for sterilisation and be connected via a manual isolating valve. Piping Each vacuum pump is shipped with loose inlet and outlet NTP flange adapters and loose inlet valve. Control System The Central Control System shall provide an intelligent human machine interface incorporating on board flash memory and realtime clock for recording operational parameters in the in built event log. The Central Control System shall operate at low voltage and include BMS connection for common fault. Visualisation of plant inputs, outputs and status through a web browser, using a simple Ethernet connection shall be available. The central control unit shall incorporate a user friendly 5.7" high-definition colour display with clear pictograms and LED indicators, providing easy access to system operational information. Cascading of vacuum pumps shall be achieved by measuring the vacuum level at the plant inlet with a pressure transducer. A mechanical back-up facility shall ensure continued operation in the event of a control system malfunction. The control system shall normally employ automatic rotation of the lead pump to maximise pump life and ensure even wear. Atlas Copco Ltd. trading as Atlas Copco Medical Unit 18 Nuffield Way, Abingdon, Oxfordshire, UK OX14 1RL www.beaconmedaes.
Open the catalog to page 1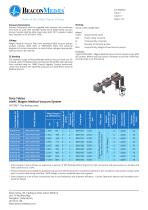
Part of the Atlas Copco Group Vacuum Receiver(s) Vacuum Receiver(s) shall be supplied with relevant test certificates and sized to wotk with Variable Speed Drive (VSD) based vacuum pumps. Vessels shall be Atlas Copco grey (RAL 7011) powder coated steel receivers to BS EN 286-1:1998. Voltage Magnis Medical Vacuum Plant and individual MGS vacuum pumps accepts 3-phase, 400V 50Hz or 380V/460V 60Hz. See electrical diagram for correct connection. In case of other voltages, appropriate options have to be ordered. CE Marking The standard range of BeaconMedss Medical Vacuum Plant are 'CE' marked...
Open the catalog to page 2All BeaconMedaes catalogs and technical brochures
-
Series B Premium
3 Pages
-
Local alarm
4 Pages
-
Central alarm
4 Pages
-
Digital Medical Gas Alarms
4 Pages
-
Zone Valve Boxes
4 Pages
-
mVAC Medical Vacuum Systems
8 Pages
-
Medical Scroll Air Retrofit
4 Pages
-
Ceiling Columns
2 Pages
-
Medical Vacuum Filters
4 Pages
-
Claw Medical Vacuum
8 Pages
-
Hose Assemblies
2 Pages
-
Biomaster Additive
4 Pages
-
Medical Gas Outlets
4 Pages
-
Lifeline Manifolds
4 Pages
-
Medical Equipment Air
8 Pages
-
Medical Instrument Air
4 Pages
-
ZMED Medical Air Systems
6 Pages
-
Scroll Medical Air Systems
8 Pages
-
Medical Air Dryers
2 Pages
-
Magnis MSV
2 Pages
-
mVAC
12 Pages
-
Lifeline® MCS
5 Pages
-
VAV05D-060H-D_V
4 Pages
-
VHV05D-060H-D_V
4 Pages
-
Medical Gas Retrofit Alarm
2 Pages
Archived catalogs
-
Medical Gas Alarm Systems
4 Pages
-
Medical Gas Outlets_2009
4 Pages
-
Oxygen and Air Flowmeters
2 Pages
-
Suction & Oxygen Therapy
2 Pages
-
Medical Air Desiccant Dryers
2 Pages
-
Instrument Air White Paper
39 Pages
-
Z MED Medical Air Systems
6 Pages
-
Claw Vacuum System
6 Pages