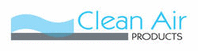
Catalog excerpts

Series 1414 Wet Process Station General Description Construction The design of the wet process station cabinet has evolved into an aerodynamic shell that efficiently utilizes the laminar air flow of the facility, thus decreasing vortices that may cause particle fallout over the process deck. Along with the evolutionary design of the station shell for particle reduction, the design has greatly improved the efficiency in exhausted air. With the greater production demand, the design has taken into consideration the need for the continuous attention toward safety. Clean Air Systems pays close attention to processor position, product flow, and placement in the design of each deck layout. Along with design, the material makeup of the stations’ shell is taken into consideration. White stress relieved polypropylene, natural polypropylene, fire retardant polypropylene, polyvinyl chloride, polyvinylidiene fluoride, and stainless steel are standard construction materials used in conjunction and consideration with process chemicals, and construction safety codes. Manufacturing of the stations’ shell, component assembly, and installation is done within a cleanroom environment. Air flow and exhaust testing is done in a controlled filtered room to Manual Wet Process Station/ Reduced Particle Generation State-of-the-art semiconductor facilities are demanding greater capacity and efficiencies. Along with economics from the wet process station manufacturers. The drive is to integrate components into a total process system designed for low defects in the submicron process era. Automation is a key factor in reducing particles and assuring process uniformity, but many semiconductor manufacturers cannot afford the expense that automation represents in today’s market. The actual run time on the automated station has yet to be faithful. Cost and reliability has prevented many semiconductor manufacturers from moving toward automation. This factor has placed the demand for low particulate wet processing with greater capacity in the conventional manual mode of operation. In order to meet this demand, Clean Air Systems has given critical attention to the design and assembly in the wet process station manufacturing practices. Clean Air Systems is a joint corporation with Clean Air Products. Clean Air Products manufacturers modular cleanrooms. The expertise of Clean Air Products engineering and manufacturing standards greatly support Clean Air Systems in the proper design of processing stations and how they are to contribute to the end result toward low defects within a cleanroom environment. Within a manual mode operation, the human operator is the major generator of airborne particulate. To decrease the airborne particulate, it has been the practice to remove the number of operators within the process area. Competition and demand has created the need for greater capacity for product flow, thus creating greater demand on the operator. This demand pinpoints the need for the process station to be efficient and safe. In order to get the total capabilities of the process station, one must look at the individual components and the design of the stations’ shell. This total is the result of twenty years of Clean Air Systems experience in particle control. For more information or to download or fax this product from the web, simply go to: www.cleanairproducts.com/1414
Open the catalog to page 1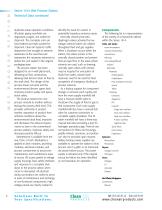
Series 1414 Wet Process Station Technical Data continued duplicate actual operation conditions. All plastic piping manifolds are degreased, purged, and sealed for shipment. The complete units are hand bathed and triple packed for shipment. Clean Air Systems’ traffic department has brought an extreme awareness to the over-the-road transporter, the necessary extremes to deliver the unit sealed in the original packaging state. The process station has been designed for an in-wall placement, alleviating air flow construction, allowing total laminar clean air flow to the work deck. The design of...
Open the catalog to page 2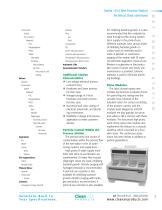
Timer: Microprocessor Counter: Microprocessor City Water DI Water Temperature: Microprocessor Microprocessor: RS232 Port Automatic Lifts Semi-Automatic Transfers Hot and/or cold Mixing Manual Pneumatic Switch Material: PVC Polypropylene PVDF Teflon Ball Needle Diaphragm Normally closed Normally open Additional Station Characteristics Low voltage electrical process control 8 hour. Headcase and lower process function case. Nitrogen purge of 8 hour headcase and lower process function case. Numerical and color coding of electrical, pneumatic, and plumbing connections. Flexibility in design and...
Open the catalog to page 3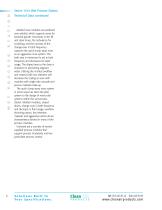
Series 1414 Wet Process Station Technical Data continued Molded rinse modules are preferred over welded, which supports areas for bacterial growth. Decreases in the fill and drain times, the turbulence for scrubbing, and the increase of the change-over in bath frequency supports the quick dump spray rinse as an aggressive rinse system. The bath area is minimized to aid in bath frequency and decreases DI water usage. The sloped area to the drain is important in preventing stagnant water. Utilizing the 4-sided overflow and material with low retention will decrease the scaling as seen with...
Open the catalog to page 4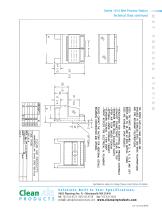
Series 1414 Wet Process Station Technical Data continued Specifications subject to change. Please contact factory for details. Solutions Built to Your Specifications. e-mail:sales@cleanairproducts.com www.cleanairproducts.com
Open the catalog to page 5All Clean Air Products catalogs and technical brochures
-
CAP-301
5 Pages
-
CAP-109BL
3 Pages
-
CAP-112
2 Pages
-
CAP-116
4 Pages
-
CAP-901
2 Pages
-
CAP-130
5 Pages
-
CAP-1532
5 Pages
-
CAP701
8 Pages
-
CAP-591
6 Pages
-
CAP-558
3 Pages
-
CAP-560
3 Pages
-
CAP-582
2 Pages
-
cap-550
4 Pages
-
cap-556
3 Pages
-
CAP-575
5 Pages
-
CAP-577
5 Pages
-
CAP1421
2 Pages
-
CAP1412
2 Pages
-
CAP-18
2 Pages
-
CAP701KD-ST
2 Pages