
Catalog excerpts
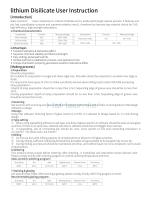
lithium Disilicate User Instruction [introduction] Glass ceramics’ main component is Lithium Disilicate and is produced through special process. It features simple, fast crystallization process and supreme esthetics result , therefore has become top material choice for CAD high efficiency, high strength restorations. 1.Chemical characteristics Composition Mass percentage Lithium oxide Silicon dioxide Aluminium oxide Potassium oxide Other oxide 2.Advantages Excellent esthetics & restorative effect. Supreme chemical stability and flexural strength. Easy milling, preserved tool life. Simple and fast crystallization process, save operation time. Unique chameleon property guarantees excellent restorative effect. Mass percentage [Making process] 1.Preparation Shoulder preparation Not suitable for preparation in angle and sharp edge area. Shoulder should be prepared to rounded inner edge or slope. It is required to have space of 1mm to make sure blocks achieve ideal milling result under CAD/CAM processing. Inlay preparation: 1.Depth of Inlay preparation should be no less than 1mm; Separating edge of groove area should be no less than 1mm. 2.Onlay preparation: depth of onlay preparation should be no less than 1mm; Separating edge of groove area should be no less than 1mm. 2.Scanning Use scanner with scanning accuracy of 20-30 um to obtain data module and transfer scanning data to CAD design software to design. 3.Design Using CAD software. Sintering factor of glass ceramics is 0.2%. It is advised to design based on 1:1 ratio during design. 4.Type setting ① When using typesetting software to set type, size data of glass ceramics in software should be same as real glass ceramics; if there is no same size, selected size data in software should be a bit bigger than real size. ② In typesetting, size of connecting bar should be cone. Cross section of one end connecting restoration is 2.5-3.0mm². The other end is 4.0-5.0mm². 5.Milling ① Do not use burs with milling capacity of 10 restorations or above to mill glass ceramics. ② During milling, sufficient milling liquid should be provided and guaranteed to be sprayed fully on bur tip. ③ During milling, air pressure should be maintained at 6-8 bar, and neither liquid nor oil is contained in air to avoid contamination. 6.Sintering This product shows purple before sintering. After sintering , it crystallizes and restoration shows desired color. Please comply strictly with sintering program to control sintering temperature and time. Glass ceramics sintering program: Start temp Start temp 7.Staining & glazing Use special Glaze Paste. After staining & glazing, please comply strictly with firing program to sinter. Recommended glazing program: 500℃
Open the catalog to page 1All HaHasmile catalogs and technical brochures
-
71mm 4D Plus Multilayer
5 Pages
-
95MM 4D Plus Multilayer
5 Pages
-
98MM 4D Plus Multilayer
5 Pages
-
95MM 4D Pro Multilayer
5 Pages
-
98MM 4D Pro Multilayer
5 Pages
-
95MM 4D Multilayer
5 Pages
-
98MM4D Multilayer
5 Pages
-
95MM UT Multilayer
4 Pages
-
98MM UT Multilayer
4 Pages
-
98MM 3D Pro Multilayer
5 Pages
-
98MM ST Multilayer
5 Pages
-
71MM ST+Color Blocks
4 Pages
-
95MM ST+Color Blocks
4 Pages
-
98MM ST+Color Blocks
4 Pages
-
71MM ST+ Blocks
4 Pages
-
95MM ST+ Blocks
4 Pages
-
98MM ST+ Blocks
4 Pages
-
71MM HT BLOCKS
4 Pages
-
95MM HT BLOCKS
4 Pages
-
98MM HT BLOCKS
4 Pages
-
Sintering Retainer Glue 10ml
1 Pages
-
HaHasmile catalogue
66 Pages