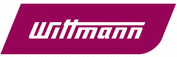

Catalog excerpts
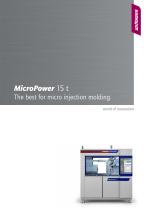
MicroPower 15 t The best for micro injection molding world of innovation
Open the catalog to page 1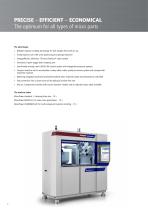
PRECISE − EFFICIENT − ECONOMICAL The optimum for all types of micro parts The advantages » Reliable injection molding technology for shot weights from 0.05 to 4 g » 2-step injection unit with screw plasticizing and plunger injection » Energy-efficient, all-electric “Drive-on-Demand“ motor system » Innovative 5-point toggle lever clamping unit » User-friendly through new UNILOG B8 control system with integrated assistance systems » Compact machine cell to accomodate a rotary table, robot, quality accurance system and conveyor belt inside the machine » Matching integrated auxiliaries...
Open the catalog to page 2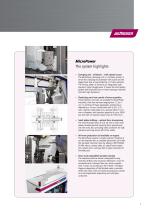
MicroPower The system highlights » Clamping unit – all-electric – with optimal access The MicroPower clamping unit is a 2-platen system, in which the clamping force between the nozzle and the toggle lever side is transmitted by a U frame element. The moving platen is driven by an integrated, highprecision 5-point toggle lever. It moves the mold platen guided with high precision on linear bearings smoothly and with high dynamism. » Plasticizing unit: best control of micro quantities Three injection unit sizes are available for MicroPower machines, with shot volumes ranging from 1.2 to 4 cm3....
Open the catalog to page 3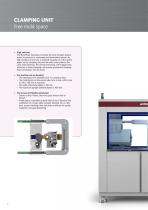
CLAMPING UNIT Free mold space » High precision The MicroPower clamping unit meets the most stringent requirements for precision in movements and automation options. Its high standard of precision is achieved by guidance of the system platen on the clamping side and the mold carrier plate on the same linear bearings. The central positioning of the toggle lever inside the U frame clamping unit ensures symmetrical clamping force transmission into the mold. » One machine size as standard – The clamping unit is available with 15 t clamping force. – The mold platens on the ejector side come in...
Open the catalog to page 4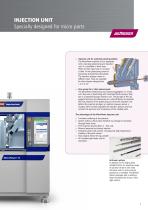
INJECTION UNIT Specially designed for micro parts » Injection unit for extremely small quantities The MicroPower injection unit is equipped with a two-step plasticizing and injection unit. It is available in three sizes. What all three sizes have in common is their 14 mm plasticizing screw for processing standard-size granulates. The injection plunger comes in different sizes. They are available for shot volumes ranging from 1.2 to 4 cm3. » One system for 3 shot volume levels The MicroPower plasticizing and injection aggregate is a 2-step unit. Step one is plasticizing with controlled back...
Open the catalog to page 5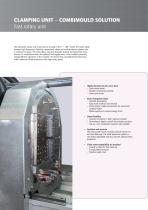
CLAMPING UNIT − COMBIMOULD SOLUTION Fast rotary unit The all-electric rotary unit is laid out for running in the +/- 180° mode. The rotary table features high dynamism, flexibility, operational safety and mold protection packed into a minimum of space. The robust basic structure provides optimal clamping force transmission. In combination with the backlash-free toggle lever, it thus enables extremely energy-efficient operation of the machine. The direct drive situated behind the rotary table combines ultimate precision with high rotary speed. » Highly dynamic electric servo drive – Short...
Open the catalog to page 6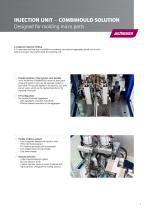
INJECTION UNIT − COMBIMOULD SOLUTION Designed for molding micro parts 2-component injection molding A 2-component machine also is available by combining two injection aggregates placed next to each other and using a rotary table inside the clamping unit. » Parallel operation of the injection units possible In the MicroPower COMBIMOULD machine, both plasticizing and injection units can be operated parallel to each other. This equally applies to the ejectors, core pulls and air valves, which can be operated parallel to the clamping movement. » H-H configuration Two parallel horizontal...
Open the catalog to page 7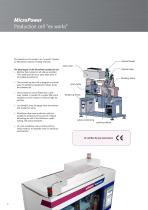
MicroPower Production cell “ex works” The production cell concept is an “ex works” solution for MicroPower injection molding machines. material feeder clean room material dryer The advantages of the MicroPower production cell » Machine frame closed on all sides as standard. Thus molding of the micro parts takes place in an isolated environment. » The enclosed machine cell is designed to provide space for additional equipment modules inside the standard cell. » The enclosed cell can be fitted with a clean room module. It consists of a suction filter and a ventilation unit for laminar air...
Open the catalog to page 8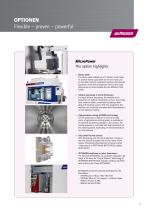
OPTIONEN Flexible – proven – powerful MicroPower The option highlights » Rotary table The rotary table enables use of 2 bottom mold halves to achieve shorter cycle times on the one hand, and on the other hand to implement insertion and removal processes. In the multi-component version, the rotary table serves to accommodate the two different mold halves. » Silicone processing in micro dimensions For liquid silicone processing, for example in the production of medical components, a micro two-component material loader is available, including a blending and metering system. With this...
Open the catalog to page 9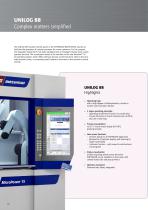
UNILOG B8 Complex matters simplified The UNILOG B8 machine control system is the WITTMANN BATTENFELD solution to facilitate the operation of complex processes for human operators. For this purpose, the integrated industrial PC has been equipped with an enlarged intuitive touch screen operator terminal. The visualization screen is the interface to the new Windows® 10 loT operating system, which offers extensive process control functions. Next to the pivotable monitor screen, a connected panel/handset is mounted on the machine’s central console. UNILOG B8 Highlights » Operating logic with a...
Open the catalog to page 10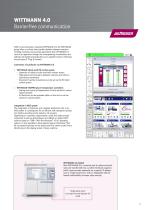
WITTMANN 4.0 Barrier-free communication With its communication standard WITTMANN 4.0, the WITTMANN group offers a uniform data transfer platform between injection molding machines and auxiliary equipment from WITTMANN. In case of an appliance change, the corresponding visualizations and settings are loaded automatically via an update function, following the principle of “Plug & Produce”. Connection of auxiliaries via WITTMANN 4.0 » WITTMANN robots with R9 control system – Operation of robots via the machine’s monitor screen – High-speed communication between machine and robot to synchronize...
Open the catalog to page 11All WITTMANN catalogs and technical brochures
-
EcoPower 55 – 550 t
17 Pages
-
SmartPower 25 – 400 t
17 Pages